A Practical Guide for Planners and Reliability Engineers
Time-based maintenance has long been the standard approach, but it isn’t always the most efficient because not all assets require the same attention; treating them equally can lead to wasted resources and unnecessary downtime. That’s where Risk-Based Maintenance (RbM) comes in.
This guide will show you how to build a risk-based maintenance program from the ground up, one that aligns with your business objectives, minimizes failure risk and optimizes maintenance investment.
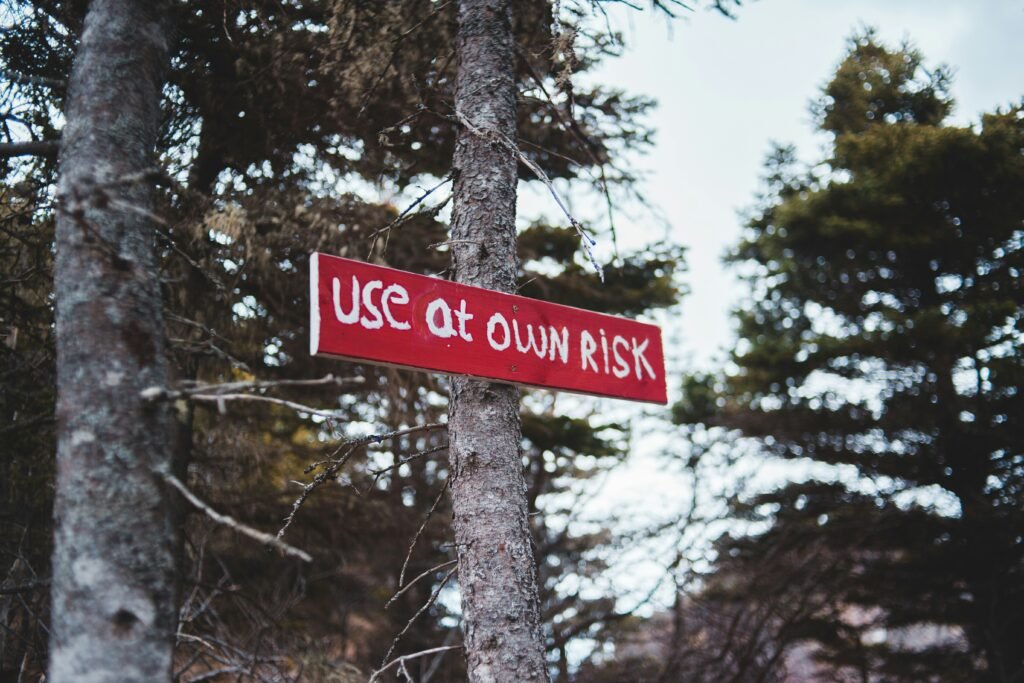
What Is Risk-Based Maintenance?
Risk-Based Maintenance (RbM) is a strategy that uses the likelihood of failure and the consequences of failure to determine how, when, and where to apply maintenance resources instead of applying the same maintenance intervals across the board. RbM allows planners to target high-risk assets with proactive strategies while reducing effort on low-impact ones.
Key Factors in RbM:
- Probability of Failure (PoF)
- Consequence of Failure (CoF)
- Asset Criticality
- Risk Priority Number (RPN)
- Detectability
Step-by-Step: How to Build Your RbM Program
Step 1: Define Maintenance Objectives
Clarify what success looks like:
- Improved asset availability?
- Lower maintenance costs?
- Safer operations?
- Regulatory compliance?
Link these goals to corporate KPIs to ensure alignment across the business.
Step 2: Conduct Asset Criticality Assessment
Score each asset using a risk matrix.
Use scales (1–5 or 1–10) for:
- Safety risk
- Downtime impact
- Repair cost
- Production loss
Assign a Probability of Failure rating
Calculate the Risk Priority Number (RPN):
RPN = CoF × PoF
Categorise assets into High, Medium, and Low Risk
Step 3: Choose Maintenance Strategies by Risk Level
Risk Level Recommended Strategy
High Predictive / Condition-Based
Medium Preventive / Interval-Based
Low Run-to-Failure
Step 4: Integrate with CMMS / EAM
Configure your asset management system to:
- Store criticality scores and risk levels
- Trigger maintenance tasks based on RPN
- Automate notifications and escalations
Step 5: Train and Align Your Team
- Educate maintenance and operations teams on RbM principles
- Clarify new workflows and responsibilities
- Involve planners, technicians, and reliability engineers.
Step 6: Review, Audit, and Improve
Use KPIs such as:
- MTBF (Mean Time Between Failures)
- MTTR (Mean Time to Repair)
- Downtime per asset
- Maintenance cost per unit produced
Reassess risk after major incidents, upgrades, or annually
Example: Bottling Plant Compressors
Compressor A: High output dependency, moderate PoF, high CoF → Condition-Based Maintenance (CBM)
Compressor B: Backup unit, low PoF and CoF → Preventive Maintenance every 6 months
Compressor C: Non-critical, infrequent use → Run-to-Failure
After 6 months, the RbM approach reduced emergency callouts by 40% and cut maintenance costs by 25%.
Risk-based maintenance helps you do more with less. Planners and engineers can reduce downtime, boost performance, and future-proof maintenance strategies by focusing on the most critical assets.
Want help rolling out RbM?
Contact us or try our free toolkit today.
#MaintenancePlanning #ReliabilityEngineering #RiskBasedMaintenance #CMMS #PdM #AssetManagement